Average Costing vs Standard Costing: Which Inventory Costing Method Is Right for Your Business?
Introduction to Inventory Costing Methods
Efficient inventory management and precise cost accounting are vital for business profitability and operational success. Of the several inventory costing methods available—including FIFO, LIFO, Average Costing, and Standard Costing—this article focuses on Average Costing and Standard Costing. These two methods are among the most widely used by small businesses, distribution companies, and manufacturing enterprises. Here, you’ll find a clear comparison, practical examples, and actionable insights to determine which method is best for your organization.
What is Average Costing?
Average Costing is an inventory valuation method where the cost of inventory is calculated as a weighted average of all inventory purchases. It’s simple to maintain and usually automated in most ERP and accounting systems, making it an ideal choice for small businesses and distributors.
How Average Costing Works (Example)
Let’s look at how Average Costing operates over several transactions, that progress over time:
Part ID | Units On Hand | Avg Cost $ | Extended $s | Note |
---|---|---|---|---|
ABC | 1,500 | $20.00 | $30,000 | Initial Stock Position |
ABC | 450 | $20.00 | $9,000 | After customer shipments |
ABC | 2,450 | $21.63 | $53,000 | After receipt of 2,000 unit Reorder at a higher price of $22.00/each, totaling $44,000 |
ABC | 1,200 | $21.63 | $25,960 | Inventory status after shipping out 1,250 more units |
ABC | 4,200 | $22.07 | 92,710 | After receipt of 3,000 unit Reorder at a even higher price of $22.25/each, totaling $66,750 |
With this last receipt, all future shipments will be costed at $22.07 each, until a new replenishment order is received. Most all ERP systems make these calculations automatically for any Inventory Item that is coded for Average Costing when new inventory is received by looking to the related PO price for the item. Subsequent to each receipt, the Average Unit Cost updated, which will be the default cost until a new replenishment cycle.
Industries Best Suited for Average Costing
- Distribution companies and any business primarily purchasing inventory for resale with minimal processing.
- Businesses looking for ease of use, as average costing requires little specialized cost accounting knowledge thanks to automated tracking by most accounting software.
Benefits of Average Costing
- Easy to implement and maintain—no specialized accounting staff needed.
- Automatically reflects changes in purchase costs over time.
- Minimizes the impact of sudden price fluctuations on reports.
- Facilitates the inclusion of fully landed costs (e.g., tariffs, freight) for more accurate gross profits.
Disadvantages of Average Costing
- Offers less granular insight into cost fluctuations and inventory performance.
- Weighted average can obscure the impact of cost changes on profit and margins.
What is Standard Costing?
Standard Costing assigns a predetermined or “standard” cost to all raw materials, subassemblies, and finished goods for a set planning period—typically a fiscal year. Actual costs are compared to these standards, and the variances are analyzed to improve operational performance.
How Standard Costing Works (Example)
- Raw Material: Cost standard set at the start of the year (e.g., $20.00/unit).
- Direct Labor: Applied using a standard hourly rate and estimated production time.
Example: $25/hour × 0.333 hours = $8.33 labor per unit. - Manufacturing Overhead: Calculated by multiplying standard hours by overhead rate (e.g., $85/hour × 0.333 hours = $28.05 overhead per unit).
- Subassembly Standard Cost: Raw Material ($20.00) + Direct Labor ($8.33) + Overhead ($28.05) = $56.38 per subassembly.
Variance Analysis in Standard Costing
Unlike Average Costing, Standard Costing supports detailed variance analysis—the comparison of actual costs with standards to drive cost control and continuous improvement.
- Purchase Price Variance (PPV): Highlights differences between standard and actual raw material purchasing costs.
- Labor and Overhead Variances: Monitor production efficiency.
Industries Best Suited for Standard Costing Costing
- Manufacturing businesses with enough resources to manage planning, standard updates, and variance analysis.
- Any organization seeking lean manufacturing processes or continuous cost improvements.
Benefits of Standard Costing
- Enables detailed variance reporting for budget and performance management.
- Clearly identifies inefficiencies in purchasing, labor, and overhead.
- Provides robust data for lean initiatives and benchmarking.
Disadvantages of Standard Costing
- Requires significant effort to establish and maintain standards (annual or more frequent reviews).
- Necessitates specialized skills such as cost accounting and manufacturing engineering.
- Outdated standards can result in inaccurate cost representation.
Key Differences: Average Costing vs. Standard Costing
Aspect |
Average Costing | Standard Costing |
Calculation Method |
Weighted average updated with each purchase | Predetermined standards, revised periodically |
Cost Updates |
Adjusts with each new receipt |
Remains fixed until standards are updated; variances posted |
Variance Analysis | No formal analysis | Detailed variance tracking is integral |
Complexity |
Simple; auto-calculated in most ERP systems |
More complex; needs regular review and expertise |
Reporting |
Reflects actual price fluctuations | Focuses on performance, control, and continuous improvement |
When to Use Each Method
Average Costing:
-
- Ideal for new or small businesses, distributors, and companies seeking cost simplicity with minimal accounting staff.
- Suits operations with straightforward purchasing and resale models and no need for extensive cost performance analysis.
Standard Costing:
-
- Essential for manufacturing operations aiming for ongoing cost control, performance monitoring, and lean process improvement.
- Recommended for companies capable of maintaining and analyzing standards, particularly as operational complexity grows.
Conclusion: Choosing the Best Inventory Costing Method
Effective inventory management hinges on selecting the right costing method for your business size, industry, and goals.
- Average Costing is fast, automated, and best for distribution and small businesses.
- Standard Costing provides richer insights for manufacturers but requires more expertise and regular attention.
Accurate inventory unit costs are central to sound pricing, profitability, and operational decisions. Companies should start with Average Costing for simplicity, then consider transitioning to Standard Costing as their operations and cost management needs evolve.
Frequently Asked Questions about Inventory Costing Methods
Q: Which costing method is easiest for startups or small businesses?
A: Average Costing is easiest, usually requires no cost accounting staff, and is supported by most accounting software.
Q: When should a business switch to Standard Costing?
A: When manufacturing complexity, need for continuous cost improvement, or lean operational initiatives become priorities.
Q: What industries use Standard Costing most?
A: Manufacturing, especially those aiming for tight cost control and process improvement.
If you are a business owner that is looking for ways to leverage your Cost Accounting capabilities, please contact us today.
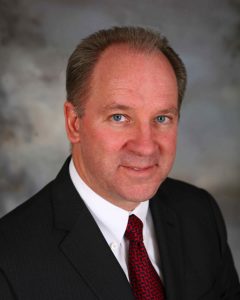
Other relevant posts: